Author: Heike Brueckner
How were corpses preserved for wakes in the 1870s? Connecticut Historical Society, UConn explain
Climate Venture Studio: A Comprehensive, Collaborative Approach to a Cleaner Planet
UConn Names Radenka Maric as 17th President
Welcome Digital Media and Design, Master of Fine Arts Students
X-Ray Vision: A Look Into the Past
Fall Semester 2022 Course: Technology Innovation & Entrepreneurship I.
UConn graduates and undergraduates are invited to enroll in the Fall Semester 2022 course, “Technology Innovation & Entrepreneurship I.”
Students taking this course have successfully launched student tech startups that later participated in entrepreneurship programs at UConn and beyond.
3D Printing Focused Industry-University Collaborative Research Center Reunites at Tech Park
SHAP3D held their eighth bi-annual Industrial Advisory Board Meeting on May 25 – May 26, 2022, at the Innovation Partnership Building (IPB) | UConn Tech Park.
“It is wonderful to reunite with the SHAP3D family and interact with new center members for the first time in person since they have joined after the pandemic began,” says Prof. Anson Ma, UConn Site Director of the SHAP3D center.
SHAP3D is a collaboration between the University of Massachusetts Lowell, University of Connecticut and Georgia Institute of Technology to create a National Science Foundation I/UCRC focused on 3D printing. The mission of the SHAP3D Center is to perform pre-competitive research providing the fundamental knowledge for 3D printing heterogeneous products that integrate multiple engineering materials with complex 3D structures and diverse functionality. The Center’s diverse membership comprises material developers, 3D printer manufacturers, 3D printing end users, and federal agencies with a stake in the growth of this emerging manufacturing platform.
The meeting was attended by more than 55 faculty members, students, and representatives from private companies, and government agencies. At this meeting, project teams currently funded by the SHAP3D center shared their progress and latest findings. Other highlights of the meeting included rapid fire presentations from members and two invited talks by Professor Timothy Long from the Arizona State University and Professor Matthew Becker from Duke University. UConn SHAP3D site, Proof of Concept Center (POCC), and Pratt & Whitney Additive Manufacturing Center (PW AMC) were all featured in the IPB lab tour. During the reception sponsored by UConn School of Engineering, students who are involved in SHAP3D projects also had the valuable opportunity to present their posters and network with the advisory board members.
Leveraging Stratasys Objet 500 Connex to Advance Multi-material 3D Printing
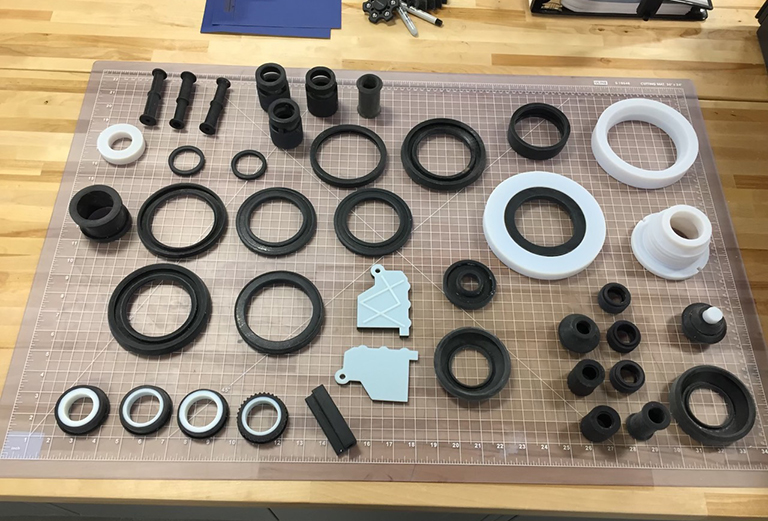
The month of May brought an advanced 3D printer, the Stratasys Objet 500 Connex, to the Science of Heterogeneous Additive Printing of 3D Materials (SHAP3D) lab in IPB. “We are extremely excited about bringing this state-of-the-art 3D printer to IPB and leveraging it to accelerate our multi-material printing research,” says Professor Anson Ma, SHAP3D UConn Site Director. The printer works by jetting and combining different print materials with high precision, thereby achieving a wide range of physical properties through changing the digital print design. This printer also complements the advanced prototyping capabilities that already exist at IPB’s Proof of Concept Center (POCC), directed by Joe Luciani.
Now armed with this powerful printer, Prof. Ma and team aim to expand the choice of materials that can be printed using this machine. Of interest are functional materials with excellent mechanical, thermal and electrical properties. Another topic of interest is to develop in-situ metrology for monitoring the print process in real time and ensuring the quality of 3D printed parts. This is especially important for high performance applications, such as aerospace, where the printed parts must meet stringent requirements. Ideally, all the printed parts must be qualified as they are produced, termed “born-qualified.” Prof. Ma’s long-term ambition is to develop autonomous 3D printers that are intelligent, through working closely with machine learning experts like Prof. Qian Yang from the Department of Computer Science and Engineering at UConn.
In addition to aerospace, the auto industry, and other major manufacturing sectors, organizations that will benefit from the SHAP3D research include 3D printer manufacturers and material suppliers. As the SHAP3D team continues to expand the material selection and improve the robustness of 3D printing, more application opportunities will open up. Professor Ma is eager to get started, although he cautions, “before we can run, we need to learn how to walk.” With the addition of the Objet 500 Connex, the SHAP3D team will be sprinting soon.
Science of Heterogeneous Additive Printing of 3D Materials (SHAP3D) is an Industry/University Cooperative Research Center (I/UCRC) funded by the National Science Foundation to catalyze the technological development of additive manufacturing, also known as 3D printing. The partners are University of Massachusetts at Lowell (UML), University of Connecticut (UC), and Georgia Institute of Technology (GT). Established in July 2018.
How Joining the Center for Material Processing Data Can Improve Your Company’s Performance
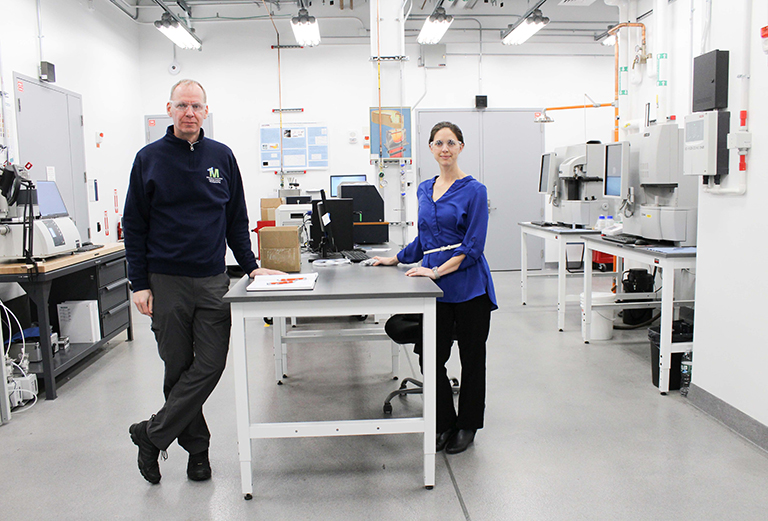
Manufacturing is changing. More demanding applications have pushed chemistries to their limits and increased the need for process modeling and digital twin analysis across industries. These modeling methods are improving in sophistication, but they are only as accurate as the data used for their calculations. No longer are assumptions of static material properties sufficient to keep up with the needs of industry. The limits of the current data are driving cost increases across industry in the direct costs of materials as well as indirect costs in performance and product sustainability.
The Center for Materials Processing Data (CMPD)* was formed in 2019 to address these challenges. CMPD is a member-driven research center dedicated to producing and collecting pre-competitive transient material property data used in materials process simulations. CMPD is a consortium of key academic and industry organizations with the goal of providing this transient materials data to the materials community for improved modeling of materials and process design.
CMPD’s pilot project has focused on material flow stress behavior as a function of strain rate, temperature, and prior microstructure for several common industry alloys. The resulting data was shared directly with industry partners as well as with ASM international’s data ecosystem for access by future members. Members benefit from unlimited non-exclusive access to all resulting process data, shared prioritization and management of data development projects, and proposal rights for new data generation projects. Following a successful preliminary test run, CMPD is now seeking additional industrial members to join the likes of industry partners Pratt & Whitney, Collins Aerospace, and Timken to help build the next generation of materials data.
Position your company for success. Join CMPD! Click here to request more information.
*UConn, WPI, and the University of Buffalo along with founding industry partners Pratt & Whitney, Collins Aerospace, and Timken partnered with ASM international in 2019 to form CMPD. For more information, visit the ASM website.